WhatsApp: 86-13735815206 / 86-17392256505
WeChat: 86-13735815206 / 86-17392256505
Phone: 86-29-88680837
Mail: sales@hlsolidscontrol.com
Add: Room 804, Building 1, Western Cloud Valley Phase II, Fengxi New Town, Xixian New District, Shaanxi Province
WeChat: 86-13735815206 / 86-17392256505
Phone: 86-29-88680837
Mail: sales@hlsolidscontrol.com
Add: Room 804, Building 1, Western Cloud Valley Phase II, Fengxi New Town, Xixian New District, Shaanxi Province
How to deal with the blockage of Shale Shaker mesh
Time: 2024-05-17 Source: Solids Control Equipment Author: Mrek
As an important solid control equipment in the oil drilling, mineral processing, power and chemical industries, Shale Shaker often have various faults that affect their use. There are usually several ways to deal with the blockage of Shale Shaker mesh.
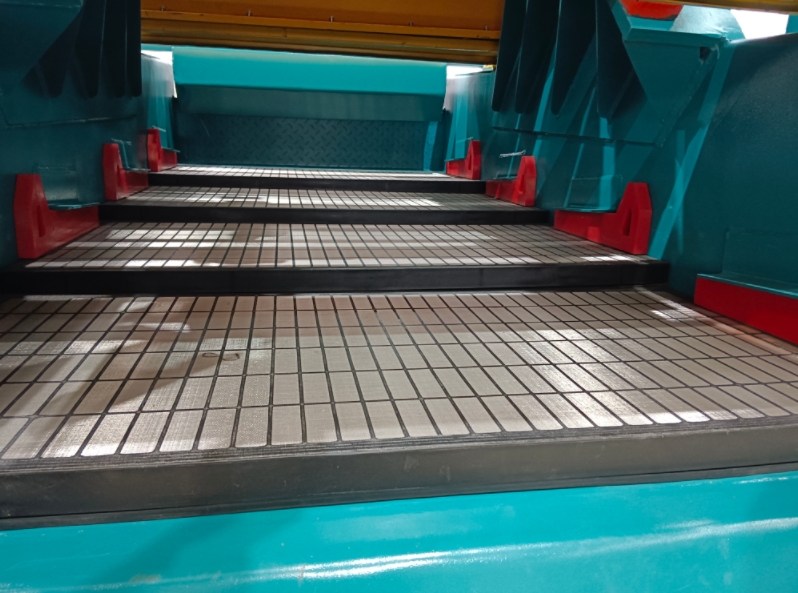
When the Shale Shaker is in normal operation, due to the various characteristics of the material, different shapes will cause various forms of mesh blockage. Blockage is usually caused by factors such as high water content of the material, static electricity, fiber content of the material, more flake particles, too coarse wire diameter of the woven screen, a large number of particles close to the separation point, spherical particles, and unreasonable screen mesh.
To prevent the Shale Shaker mesh from being blocked, the screen mesh should be cleaned first, and then the water spray volume and screen surface inclination angle should be adjusted appropriately.
When the material particle size is fine, the mud content is high, and the screening particle size is small, the moisture plays a decisive role in the blockage of the screen. When the moisture content in the material is greater than 5%, if there is no condition to dry the material, the screen surface and screen mesh should be selected in a targeted manner.
When the moisture content is greater than 8%, wet screening should be used. For materials with more flaky particles, it is necessary to change the material crushing method and the particle size matching of different crushing methods.
In addition, reasonable adjustment of the screen tension is an effective way to reduce screen blockage. Reasonable tension causes the screen and the support beam to produce slight secondary vibration, thereby effectively reducing the occurrence of blockage. The specific method is to make the tension hook into a constant force tensioning mechanism, that is, to install a spring on the tensioning bolt, so as to achieve the purpose of reducing screen blockage.
In the daily use of Shale Shaker, in order to avoid the occurrence of Shale Shaker failures, regular maintenance and observation of the equipment should be strengthened, problems should be discovered in time and quickly handled, so as to effectively reduce the incidence of failures.
At the same time, when purchasing Shale Shaker, attention should be paid to the model, quality and brand of the equipment, so as to effectively save costs and reduce production accidents.
HL Petroleum is a professional solids control system provider. We have more than 20 years of research, design and manufacturing experience. HL Solids Control equipment are professional, reliable, cost-effective and customizable. It is a trustworthy brand in the industry!
HL Petroleum always opens its arms to actively promote industry exchanges and promote technological development. We welcome every customer to visit, cooperate and consult.
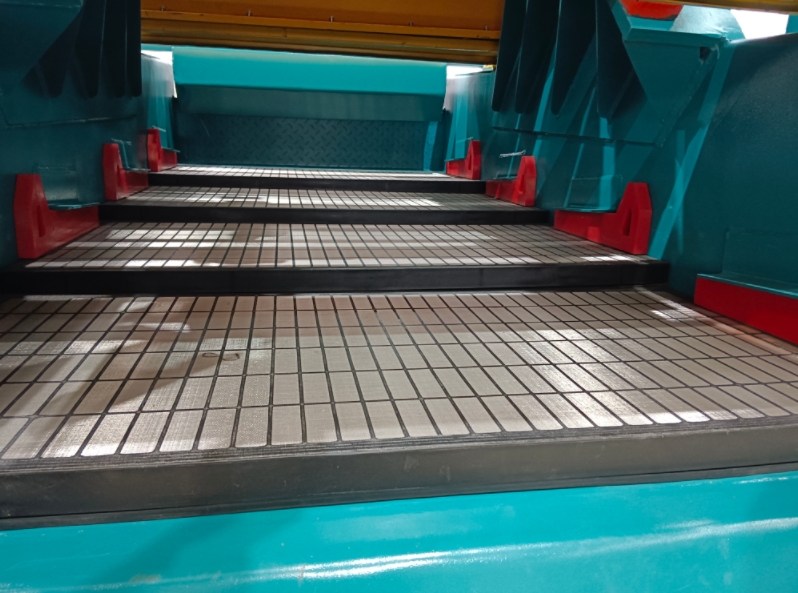
When the Shale Shaker is in normal operation, due to the various characteristics of the material, different shapes will cause various forms of mesh blockage. Blockage is usually caused by factors such as high water content of the material, static electricity, fiber content of the material, more flake particles, too coarse wire diameter of the woven screen, a large number of particles close to the separation point, spherical particles, and unreasonable screen mesh.
To prevent the Shale Shaker mesh from being blocked, the screen mesh should be cleaned first, and then the water spray volume and screen surface inclination angle should be adjusted appropriately.
When the material particle size is fine, the mud content is high, and the screening particle size is small, the moisture plays a decisive role in the blockage of the screen. When the moisture content in the material is greater than 5%, if there is no condition to dry the material, the screen surface and screen mesh should be selected in a targeted manner.
When the moisture content is greater than 8%, wet screening should be used. For materials with more flaky particles, it is necessary to change the material crushing method and the particle size matching of different crushing methods.
In addition, reasonable adjustment of the screen tension is an effective way to reduce screen blockage. Reasonable tension causes the screen and the support beam to produce slight secondary vibration, thereby effectively reducing the occurrence of blockage. The specific method is to make the tension hook into a constant force tensioning mechanism, that is, to install a spring on the tensioning bolt, so as to achieve the purpose of reducing screen blockage.
In the daily use of Shale Shaker, in order to avoid the occurrence of Shale Shaker failures, regular maintenance and observation of the equipment should be strengthened, problems should be discovered in time and quickly handled, so as to effectively reduce the incidence of failures.
At the same time, when purchasing Shale Shaker, attention should be paid to the model, quality and brand of the equipment, so as to effectively save costs and reduce production accidents.
HL Petroleum is a professional solids control system provider. We have more than 20 years of research, design and manufacturing experience. HL Solids Control equipment are professional, reliable, cost-effective and customizable. It is a trustworthy brand in the industry!
HL Petroleum always opens its arms to actively promote industry exchanges and promote technological development. We welcome every customer to visit, cooperate and consult.