WhatsApp: 86-13735815206 / 86-17392256505
WeChat: 86-13735815206 / 86-17392256505
Phone: 86-29-88680837
Mail: sales@hlsolidscontrol.com
Add: Room 804, Building 1, Western Cloud Valley Phase II, Fengxi New Town, Xixian New District, Shaanxi Province
WeChat: 86-13735815206 / 86-17392256505
Phone: 86-29-88680837
Mail: sales@hlsolidscontrol.com
Add: Room 804, Building 1, Western Cloud Valley Phase II, Fengxi New Town, Xixian New District, Shaanxi Province
A brief discussion on the current status and prospects of drilling fluid cooling technology
Time: 2024-05-10 Source: Solids Control System Author: Mrek
This study proposes a drilling fluid cooling solution that reduces drilling fluid temperature, improves wellbore stability, makes logging instruments more operable, better controls the flow of drilling fluid and reduces the amount of additives, and improves drilling operations. safety.
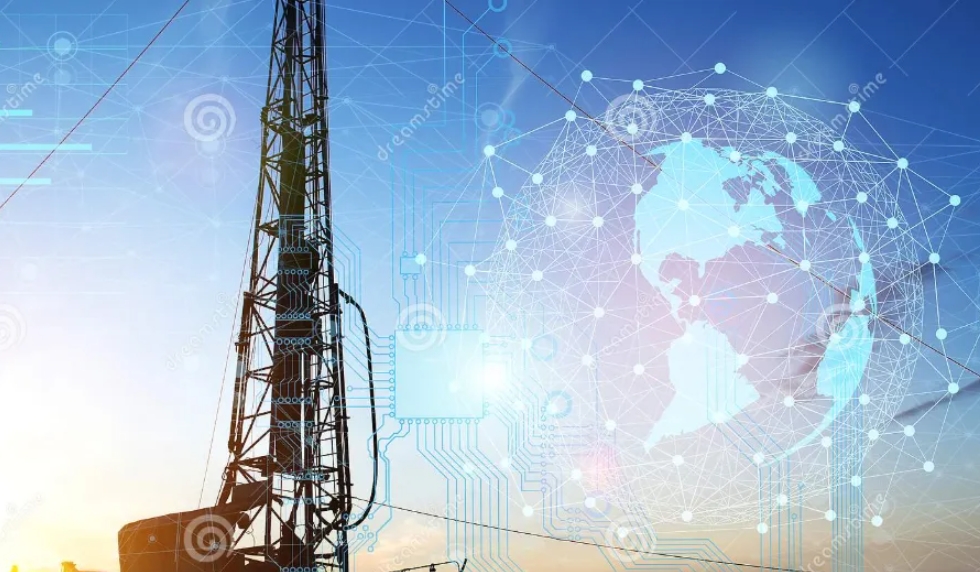
1. Development status of drilling fluid cooling technology
At present, the cooling of drilling fluid during the drilling process generally adopts natural cooling, low-temperature medium mixed cooling, cooling device cooling, etc.
natural cooling
The drilling fluid returned from the wellhead passes through the open wellhead overflow pipe, diverter box, etc. and undergoes a vibrating screen. When the drilling fluid is screened, it exchanges heat with the air and is naturally cooled down. The drilling fluid can also be naturally cooled when it is stored in the drilling tank. This This cooling method is greatly affected by environmental climate conditions and is generally used when the drilling fluid processing volume is not large and the temperature is not high.
Low temperature medium mixed cooling
When the temperature of the drilling fluid is too high, low-temperature solids or liquids are put into the drilling fluid tank and the temperature of the drilling fluid is reduced by stirring and mixing. Due to economic reasons, it is generally used in water-based drilling fluids with sufficient low-temperature water sources.
Cooling device cooling
When the temperature of the drilling fluid returned from the wellhead is too high and the previous two methods of cooling are not suitable, a cooling device can be used for forced cooling. The cooling device often uses air cooling, spraying, and interactive heat exchange.
Air cooling is to install a high-power fan next to the vibrating screen. When the vibrating screen is screening, the heat is taken away by the wind for cooling.
Spraying is to spray refrigerant or cooling water directly on the drilling fluid pipe, so that the refrigerant or cooling water takes away heat and cools the drilling fluid.
Interactive heat exchange uses a heat exchanger for heat exchange, and heat exchanges between high-temperature drilling fluid and refrigerant or cooling water in the heat exchanger to achieve cooling of the drilling fluid.
2. Drilling fluid cooling solution
In view of the technical shortcomings of the existing drilling fluid cooling equipment installed after the drilling fluid purification treatment equipment, which cannot solve the technical shortcomings of high-temperature drilling fluid adversely affecting the service life of the purification equipment and the operating safety of the operators, four-stage cooling is used at the front end of the drilling fluid purification treatment equipment. It achieves the effect of rapidly cooling the drilling fluid, so that the drilling fluid is cooled to a safe temperature before entering the purification treatment equipment; this can extend the service life of the purification equipment and improve the operating safety of operators.
In order to achieve the above purpose, the following technical solutions are provided:
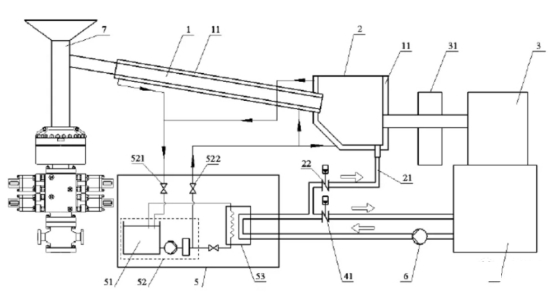
As shown in Figure 1, the drilling fluid cooling system includes a wellhead overflow pipe 1 connected to the wellhead 7, a diverter box 2 connected to the wellhead overflow pipe 1, a vibrating screen 3 connected to the diverter box 2, and a mud tank 4 connected to the vibrating screen 3. , the outer wall sleeves of the wellhead overflow pipe 1 and the diverter box 2 are equipped with heat exchange insulation layers 11, the vibrating screen side is equipped with a fan 31, and the mud tank 4 is connected to a cooling device 5; the heat exchange insulation layer 11 is used to cool the wellhead overflow The fan 31 is used to cool the drilling fluid in the pipe 1 and the diverter box 2. The cooling device 5 is used to cool the drilling fluid in the mud tank 4 and to circulate and inject cooling into the heat exchange barrier 11. Liquid 51.
The mud tank 4 is equipped with valve three 41, and the valve three 41 is used to regulate the flow of drilling fluid from the cooling device 5 to the mud tank 4.
The bottom of the diverter box 2 is connected to an auxiliary cooling pipe 21, and the other end of the auxiliary cooling pipe 21 is connected to a cooling device 5, which is used to inject the cooled drilling fluid into the diverter box 2 to reduce the temperature of the drilling fluid in the diverter box 2; auxiliary The cooling pipeline 21 is equipped with a valve 22, which is used to regulate the flow of drilling fluid from the cooling device 5 to the diverter box 2.
Four-stage cooling is achieved, and one-stage cooling is achieved: The heat exchange insulation layer 11 set on the outer wall of the wellhead overflow pipe 1 takes away the heat of the high-temperature drilling fluid in the wellhead overflow pipe 1 through the heat exchange principle to achieve one-stage cooling; two-stage cooling: The heat exchange barrier 11 set on the outer wall of the diverter box 2 takes away the heat of the high-temperature drilling fluid in the diverter box 2 through the heat exchange principle to achieve secondary cooling; third-stage cooling: use the fan 31 to blow the screen surface of the vibrating screen 3, with The heat of the high-temperature drilling fluid on the screen surface is taken away to achieve three-stage cooling; four-stage cooling: the cooling device 5 takes away the heat of the drilling fluid in the mud tank 4 to achieve four-stage cooling.
Option II:
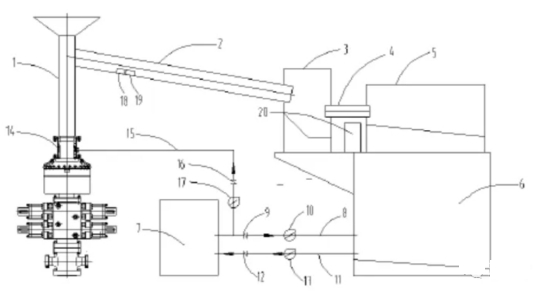

1-Wellhead bell mouth; 2-Wellhead overflow pipe; 3-Diverter box 4-Diverter pipeline; 5-Vibrating screen; 6-Drilling fluid tank; 7-Cooling unit; 8-Pipeline one; 9-Valve one; 10- Pump one; 11-pipeline two; 12-valve two; 13-pump two; 14-cooling mixer; 15-pipeline three; 16-valve three; 17-pump three; 18-temperature sensor; 19-flow sensor; 20 -Cooling fan
The drilling fluid returned from the wellhead flows into the wellhead overflow pipe 2 through the wellhead bell mouth 1, and the temperature of the drilling fluid is detected through the temperature sensor 18. When the temperature of the drilling fluid exceeds the preset temperature, the cooling mixer 14 is opened, and valves 3 and 16 are opened. Pump three 17 makes the low-temperature drilling fluid of the cooling unit enter the cooling mixer 14 through pipeline three. The low-temperature drilling fluid enters the annular space formed by the inner casing one, the inner casing two and the inner wall of the outer casing from the low-temperature drilling fluid interface, so that the low-temperature drilling fluid becomes The jet is mixed with high-temperature drilling fluid, thereby effectively reducing the temperature of the high-temperature drilling fluid. The cooled and mixed drilling fluid enters the wellhead overflow pipe through the wellhead bell mouth. When it flows through the flow sensor, the drilling fluid flow rate is detected. By adjusting the low-temperature drilling fluid The flow rate of the drilling fluid is used to control the overall drilling fluid flow entering the diverter box. The cooled and mixed drilling fluid enters the diverter box 3 from the wellhead overflow pipe 2, and then enters the purification equipment for purification. Through the cooling fan, the drilling fluid on the vibrating screen surface is The liquid is subjected to air blowing and cooling treatment, and a secondary cooling is performed to further reduce the temperature of the drilling fluid. The purified drilling fluid enters the drilling fluid tank 6, and enters the cooling unit 7 from the drilling fluid tank 6. It is cooled three times, and the drilling fluid entering the cooling unit passes through Perform heat exchange with the cooling medium to achieve cooling effect.
The increase in formation temperature will cause the drilling fluid to undergo high-temperature degradation, high-temperature cross-linking, high-temperature desorption and other phenomena, seriously affecting the performance of the drilling fluid and the service life of downhole tools, and even causing accidents in the well, threatening the safety of drilling operations and personnel safety. During drilling operations, It is very necessary to cool the drilling fluid to the appropriate temperature in time.
Drilling fluid cooling is mainly used in China after the purification is completed and before the mud pump is pumped into the bottom of the well. There is little research on cooling in front of the purification equipment. In order to improve the operating safety of operators, it is recommended to conduct such research as soon as possible. Source: youmeifang
HL Petroleum is a professional solids control system provider. We have more than 20 years of research, design and manufacturing experience. The main products include Mud Shale Shaker, Vacuum Degasser,Mud Cleaner, Centrifuge,mud agitators, Mud Gun,jet Mud Mixer,Centrifugal Pumps, Shear Pump, Spray Pumps,Vacuum Pump,Mud Gas Separator etc.
HL Petroleum has been committed to solving problems such as mud solid-liquid separation, mud treatment, and tail mud environmental protection treatment in the field of deep oil field mining. It is a trustworthy brand in the industry!
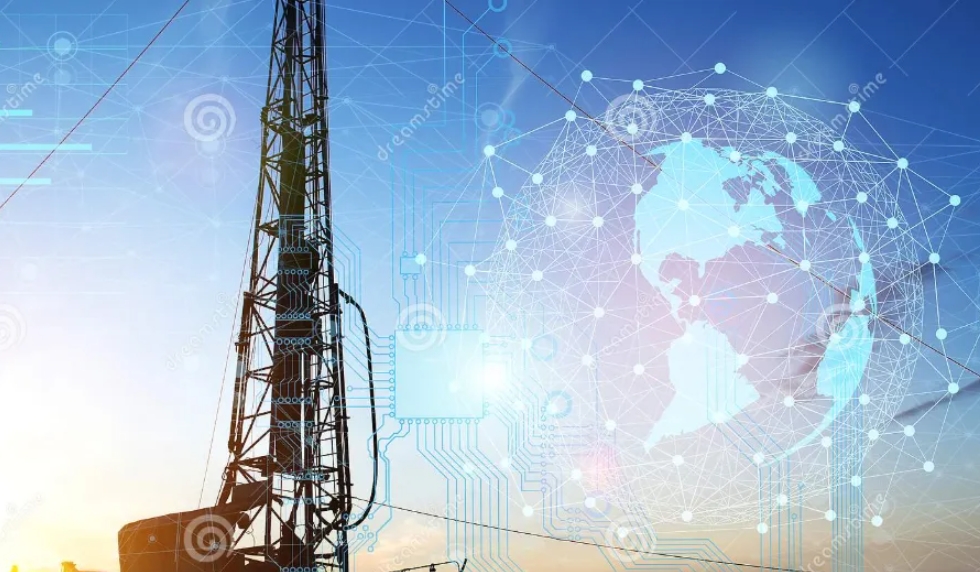
1. Development status of drilling fluid cooling technology
At present, the cooling of drilling fluid during the drilling process generally adopts natural cooling, low-temperature medium mixed cooling, cooling device cooling, etc.
natural cooling
The drilling fluid returned from the wellhead passes through the open wellhead overflow pipe, diverter box, etc. and undergoes a vibrating screen. When the drilling fluid is screened, it exchanges heat with the air and is naturally cooled down. The drilling fluid can also be naturally cooled when it is stored in the drilling tank. This This cooling method is greatly affected by environmental climate conditions and is generally used when the drilling fluid processing volume is not large and the temperature is not high.
Low temperature medium mixed cooling
When the temperature of the drilling fluid is too high, low-temperature solids or liquids are put into the drilling fluid tank and the temperature of the drilling fluid is reduced by stirring and mixing. Due to economic reasons, it is generally used in water-based drilling fluids with sufficient low-temperature water sources.
Cooling device cooling
When the temperature of the drilling fluid returned from the wellhead is too high and the previous two methods of cooling are not suitable, a cooling device can be used for forced cooling. The cooling device often uses air cooling, spraying, and interactive heat exchange.
Air cooling is to install a high-power fan next to the vibrating screen. When the vibrating screen is screening, the heat is taken away by the wind for cooling.
Spraying is to spray refrigerant or cooling water directly on the drilling fluid pipe, so that the refrigerant or cooling water takes away heat and cools the drilling fluid.
Interactive heat exchange uses a heat exchanger for heat exchange, and heat exchanges between high-temperature drilling fluid and refrigerant or cooling water in the heat exchanger to achieve cooling of the drilling fluid.
2. Drilling fluid cooling solution
In view of the technical shortcomings of the existing drilling fluid cooling equipment installed after the drilling fluid purification treatment equipment, which cannot solve the technical shortcomings of high-temperature drilling fluid adversely affecting the service life of the purification equipment and the operating safety of the operators, four-stage cooling is used at the front end of the drilling fluid purification treatment equipment. It achieves the effect of rapidly cooling the drilling fluid, so that the drilling fluid is cooled to a safe temperature before entering the purification treatment equipment; this can extend the service life of the purification equipment and improve the operating safety of operators.
In order to achieve the above purpose, the following technical solutions are provided:
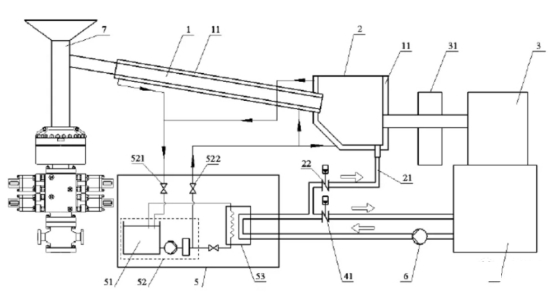
As shown in Figure 1, the drilling fluid cooling system includes a wellhead overflow pipe 1 connected to the wellhead 7, a diverter box 2 connected to the wellhead overflow pipe 1, a vibrating screen 3 connected to the diverter box 2, and a mud tank 4 connected to the vibrating screen 3. , the outer wall sleeves of the wellhead overflow pipe 1 and the diverter box 2 are equipped with heat exchange insulation layers 11, the vibrating screen side is equipped with a fan 31, and the mud tank 4 is connected to a cooling device 5; the heat exchange insulation layer 11 is used to cool the wellhead overflow The fan 31 is used to cool the drilling fluid in the pipe 1 and the diverter box 2. The cooling device 5 is used to cool the drilling fluid in the mud tank 4 and to circulate and inject cooling into the heat exchange barrier 11. Liquid 51.
The mud tank 4 is equipped with valve three 41, and the valve three 41 is used to regulate the flow of drilling fluid from the cooling device 5 to the mud tank 4.
The bottom of the diverter box 2 is connected to an auxiliary cooling pipe 21, and the other end of the auxiliary cooling pipe 21 is connected to a cooling device 5, which is used to inject the cooled drilling fluid into the diverter box 2 to reduce the temperature of the drilling fluid in the diverter box 2; auxiliary The cooling pipeline 21 is equipped with a valve 22, which is used to regulate the flow of drilling fluid from the cooling device 5 to the diverter box 2.
Four-stage cooling is achieved, and one-stage cooling is achieved: The heat exchange insulation layer 11 set on the outer wall of the wellhead overflow pipe 1 takes away the heat of the high-temperature drilling fluid in the wellhead overflow pipe 1 through the heat exchange principle to achieve one-stage cooling; two-stage cooling: The heat exchange barrier 11 set on the outer wall of the diverter box 2 takes away the heat of the high-temperature drilling fluid in the diverter box 2 through the heat exchange principle to achieve secondary cooling; third-stage cooling: use the fan 31 to blow the screen surface of the vibrating screen 3, with The heat of the high-temperature drilling fluid on the screen surface is taken away to achieve three-stage cooling; four-stage cooling: the cooling device 5 takes away the heat of the drilling fluid in the mud tank 4 to achieve four-stage cooling.
Option II:
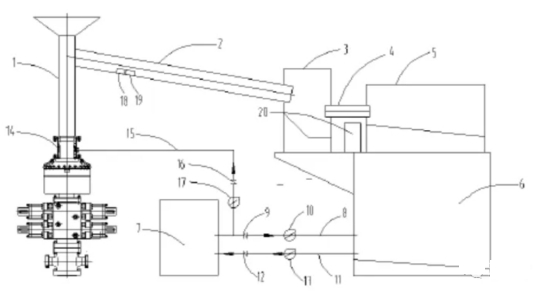

1-Wellhead bell mouth; 2-Wellhead overflow pipe; 3-Diverter box 4-Diverter pipeline; 5-Vibrating screen; 6-Drilling fluid tank; 7-Cooling unit; 8-Pipeline one; 9-Valve one; 10- Pump one; 11-pipeline two; 12-valve two; 13-pump two; 14-cooling mixer; 15-pipeline three; 16-valve three; 17-pump three; 18-temperature sensor; 19-flow sensor; 20 -Cooling fan
The drilling fluid returned from the wellhead flows into the wellhead overflow pipe 2 through the wellhead bell mouth 1, and the temperature of the drilling fluid is detected through the temperature sensor 18. When the temperature of the drilling fluid exceeds the preset temperature, the cooling mixer 14 is opened, and valves 3 and 16 are opened. Pump three 17 makes the low-temperature drilling fluid of the cooling unit enter the cooling mixer 14 through pipeline three. The low-temperature drilling fluid enters the annular space formed by the inner casing one, the inner casing two and the inner wall of the outer casing from the low-temperature drilling fluid interface, so that the low-temperature drilling fluid becomes The jet is mixed with high-temperature drilling fluid, thereby effectively reducing the temperature of the high-temperature drilling fluid. The cooled and mixed drilling fluid enters the wellhead overflow pipe through the wellhead bell mouth. When it flows through the flow sensor, the drilling fluid flow rate is detected. By adjusting the low-temperature drilling fluid The flow rate of the drilling fluid is used to control the overall drilling fluid flow entering the diverter box. The cooled and mixed drilling fluid enters the diverter box 3 from the wellhead overflow pipe 2, and then enters the purification equipment for purification. Through the cooling fan, the drilling fluid on the vibrating screen surface is The liquid is subjected to air blowing and cooling treatment, and a secondary cooling is performed to further reduce the temperature of the drilling fluid. The purified drilling fluid enters the drilling fluid tank 6, and enters the cooling unit 7 from the drilling fluid tank 6. It is cooled three times, and the drilling fluid entering the cooling unit passes through Perform heat exchange with the cooling medium to achieve cooling effect.
The increase in formation temperature will cause the drilling fluid to undergo high-temperature degradation, high-temperature cross-linking, high-temperature desorption and other phenomena, seriously affecting the performance of the drilling fluid and the service life of downhole tools, and even causing accidents in the well, threatening the safety of drilling operations and personnel safety. During drilling operations, It is very necessary to cool the drilling fluid to the appropriate temperature in time.
Drilling fluid cooling is mainly used in China after the purification is completed and before the mud pump is pumped into the bottom of the well. There is little research on cooling in front of the purification equipment. In order to improve the operating safety of operators, it is recommended to conduct such research as soon as possible. Source: youmeifang
HL Petroleum is a professional solids control system provider. We have more than 20 years of research, design and manufacturing experience. The main products include Mud Shale Shaker, Vacuum Degasser,Mud Cleaner, Centrifuge,mud agitators, Mud Gun,jet Mud Mixer,Centrifugal Pumps, Shear Pump, Spray Pumps,Vacuum Pump,Mud Gas Separator etc.
HL Petroleum has been committed to solving problems such as mud solid-liquid separation, mud treatment, and tail mud environmental protection treatment in the field of deep oil field mining. It is a trustworthy brand in the industry!