WhatsApp: 86-13735815206 / 86-17392256505
WeChat: 86-13735815206 / 86-17392256505
Phone: 86-29-88680837
Mail: sales@hlsolidscontrol.com
Add: Room 804, Building 1, Western Cloud Valley Phase II, Fengxi New Town, Xixian New District, Shaanxi Province
WeChat: 86-13735815206 / 86-17392256505
Phone: 86-29-88680837
Mail: sales@hlsolidscontrol.com
Add: Room 804, Building 1, Western Cloud Valley Phase II, Fengxi New Town, Xixian New District, Shaanxi Province
Discussion on the rationality of supporting the deep well drilling fluid solids control system
Time: 2024-05-08 Source: Author:
With the rapid development of new drilling technologies and processes, safe, efficient and low-cost drilling of deep and ultra-deep wells has become an inevitable trend. High standards of drilling fluid performance are the prerequisite and guarantee for the smooth implementation of drilling.In order to balance formation pressure, weighting agents are commonly used in ultra-deep well drilling fluids, accounting for more than 50% of the solid phase volume fraction. The cost of solid phase additives accounts for more than 75% of the total cost of drilling fluids, which sharply increases the cost of drilling fluids.
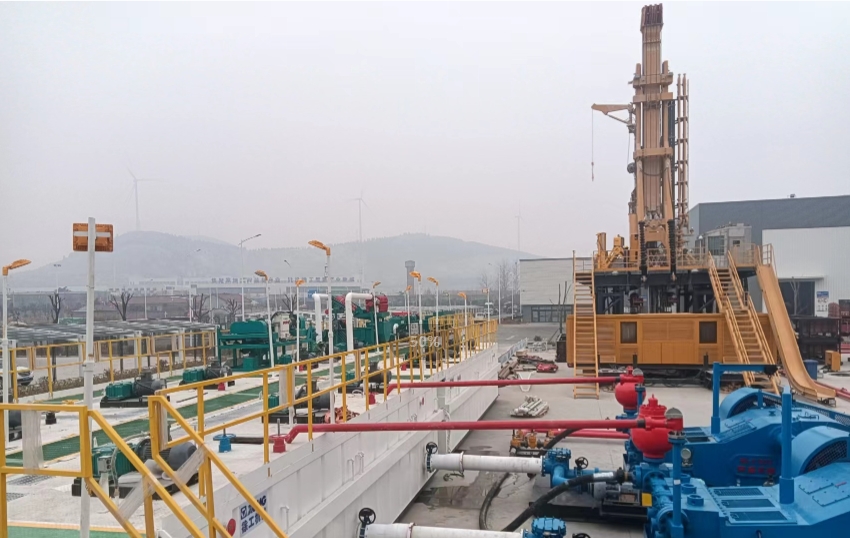
The increase of weighting agent in drilling fluid increases the viscosity and shear force of the drilling fluid, making it more difficult to control the performance of the drilling fluid. Efficient recovery of weighting agents is not only the basic prerequisite to ensure the performance of drilling fluids, but also an effective way to control the cost of drilling fluids.
At present, the effect of using solid control equipment in ultra-deep wells is not ideal. Optimizing the solid control system is an effective measure to improve solid control efficiency and reduce the comprehensive cost of solid control. Based on the research of international scholars, the author has carried out a study on the solid control system of drilling fluid for ultra-deep wells. The rationality of supporting facilities was studied, and the proposed optimized solids control system has significant economic benefits and environmental protection effects.
1. Analysis of solid particles and formation characteristics of drilling fluid system
1.1 Analysis of solid particles in drilling fluid system
Useful solid phases in drilling fluids mainly include bentonite, solid phase weighting agents and additives. To retain useful solid phases and remove harmful solid phases, it is necessary to select appropriate solid control equipment based on the solid phase content and particle size distribution characteristics of the drilling fluid. Therefore, a well-designed solids control process is the basic prerequisite for effective removal of harmful solids and efficient recovery of useful solids.
During the drilling process of deep wells and ultra-deep wells of 4 500 to 9 000 m, barite with a particle size distribution of 10 to 100 μm accounts for more than 80% of the total barite in the drilling fluid; barite with a particle size distribution of 10 to 100 μm Iron ore accounts for about 85% of the total hematite; the bentonite particle size is mainly distributed in the range of 0.01~1 μm. Special attention needs to be paid to recovering weighting agents with a particle size distribution of 10 to 100 μm in solid control systems. Different solid control equipment is selected according to different particle sizes. In the particle size range of 540~800 μm, a 30~50 mesh vibrating screen is used. In the 140~540 μm range, an 80~100 mesh vibrating screen is used. In the 40~140 μm range, a sand remover is selected. , a desilter is used in the 7~40 μm range, and a centrifuge is used in the remaining parts. This kind of matching, whether it is the range of solid phase particle size that various equipment can separate, or the processing capacity of various equipment, is adapted to the solid phase content and particle size distribution of the drilling fluid, and the workload is relatively balanced.
1.2 Analysis of formation characteristics
Taking the 6 000 m and 7 000 m ultra-deep wells in an oil field in China as an example, as the formation depth increases, the drilling fluid density also increases correspondingly, reaching a maximum of about 2.35 g/cm 3 . In ultra-deep wells of 6 000 m and above Weighted oil-based drilling fluid is used to improve the ability to lubricate and carry cuttings to stabilize the well wall and balance the bottom hole formation pressure.
Analyze the particle size and characteristics of drill cuttings in different opening sections. In the upper section of the first and second openings, the formation is shallow, and most solid particles are concentrated in the range of 30 to 300 μm in size, of which more than 80% are particles larger than 200 μm. Large-size solid particles can easily cause drill bit and The wear of the drill string reduces the mechanical penetration rate; in the middle and lower sections of the second opening, the drilling cuttings mostly exist in the drilling fluid in the form of coarse sand grains, fine sand grains, mud grains, etc. Due to the large amount of mud grains, filter cake may be formed. It is easy to cause differential pressure stuck; in the third well section, drilling cuttings particles mainly exist in the drilling fluid in the form of sand grains, mud particles and clay particles, causing reservoir damage and wellbore instability. The barite content in the drilling fluid High, the density is relatively high; in the fourth well section and below, most of the drilling cuttings particles are mud particles and clay particles. The clay particles increase the viscosity of the drilling fluid, resulting in large flow resistance, reduced effective power, reduced drilling speed, and also It is possible for the drill bit to become mud-packed, which increases the range of pressure changes and can easily cause accidents such as spraying, leakage, collapse, and jamming.
Ultra-deep well solids control systems need to efficiently recover high-cost weighting agents, simultaneously process and recover oil-based drilling fluids, and effectively remove harmful solid particles to ensure the safety and smooth progress of the drilling process. This puts relatively high requirements on the performance of ultra-deep well solid control systems.
2. Analysis of oilfield on-site solids control system problems
The four-level solids control system currently used in oil fields (the four-level solids control discussed in this article does not include degasser) has not achieved the expected results. The main problems are as follows:
(1) The Shale Shaker is a full-displacement processing equipment. When the processing capacity of a single unit does not reach the maximum bottom-hole return volume, it is easy to cause slurry running. At the same time, the splashing is serious during the treatment process; the vibrating screen mesh is prone to local damage, resulting in The separation efficiency is poor; after large particles of drill cuttings pass through the vibrating screen, they add extra load to equipment such as desanders, desilters, and centrifuges.
(2) The solid phase removal range of desanders and desilter equipment partially overlaps with that of vibrating screens and centrifuges, resulting in low overall solids control efficiency; the power consumption of the on-site solids control system is approximately 342~370 kW, and the desanders and desilters partially overlap. The power consumption of the mud filter is about 90~150 kW. The power consumption is relatively high, which leads to an increase in drilling costs. The desander and desilter equipment have a high failure rate and are prone to blockage, leakage, drum damage and other failures.
(3) The on-site configuration of the centrifuge is unreasonable, the difference between the combined speeds of the centrifuges is small, and the use effect is not good; the barite content in the removed solid phase is high, resulting in the waste of barite; the ultra-fine harmful solid phase in the drilling fluid Insufficient removal of particles causes the viscosity of the drilling fluid to continuously increase during the circulation process, affecting the normal operation of the entire solid control circulation system and the drilling process; the operation of the centrifuge is not standardized enough and the inlet flow control is not reasonable, resulting in a high failure rate of the centrifuge. .
3. Research and analysis on the reasonable configuration of ultra-deep well solid control system The current solid control process lacks pertinence
As different formations and drilling parameters change, the solids control process should also be adjusted according to the actual situation to achieve the removal and recovery functions of the solids control system in the most reasonable way.
3.1 Optimization design of solid control system
The four-level solids control system is currently the most common solids control system. The system was optimized and designed, and a two-level solid control system based on vibrating screen and centrifuge was proposed. In this system, the sand remover and silt remover are replaced by an integrated sand and mud removal machine, and an underflow screen is added at the bottom. When used, it can not only remove large particles of useless solid phase, but also recover barite particles and drilling fluid. Under normal working conditions, the integrated sand and mud removal machine is used as backup equipment and is not used by the system. When the return volume from the wellhead is large, or the vibrating screen or centrifuge fails, the integrated sand and mud removal machine is used as a backup equipment to process the drilling fluid, so that the entire solid control cycle process is continuous and uninterrupted, reaching the power consumption of the entire solid control system. Low requirements, high modularity and high reliability.
After separation, it enters the parallel multi-layer vibrating screen combination for processing. According to the actual situation, 3 to 5 vibrating screens are connected in parallel. The performance and screen mesh size of a single vibrating screen need to be based on the drilling fluid return volume and drilling fluid particle characteristics of different open section wellheads. If the returning drilling fluid particles have high humidity, a dry vibrating screen can be used if necessary.
3.2 Adaptability analysis of solids control system after optimization
(1) In the first well opening section, most of the drilling cuttings are large particles, and the return drilling fluid has a large displacement. During this period, only the parallel vibrating screen group can be used to remove large particles of cuttings. The mesh number used by the vibrating screen can be selected from 80 to 100 meshes. The separation particle size is greater than 165 μm. The critical separation particle size of the vibrating screen is 180 μm and the minimum separation particle size is 100 μm, which meets the processing capacity of drilling fluid. , and the large particles of drill cuttings were removed, and the discarded drill cuttings particles were directly discharged into the waste solid phase pool.
(2) In the middle and lower section of the second well, a parallel vibrating screen group and a medium-speed centrifuge are used together, and an integrated sand and mud removal machine is used as backup equipment. At this time, the vibrating screen mesh is selected to be 120 mesh or above, and is used with a medium-speed centrifuge or an integrated sand and mud removal machine to remove smaller solid particles in the drilling fluid to prevent them from circulating to the bottom of the well and being repeatedly worn into ultra-fine particles, thus ensuring the normal operation of the equipment. operation, extending the service life of the equipment and improving the safety factor of the entire solid control system.
(3) In the third well section, a parallel vibrating screen group and medium and high-speed centrifuges are used in combination. In this section of the well, the density of the drilling fluid is high and the barite content in the drilling fluid is high. At this time, the requirements for the removal of ultra-fine solid particles in the drilling fluid and the recovery of barite are relatively high, so it is necessary to start a medium-speed centrifuge for recovery drilling. barite in the liquid; start the high-speed centrifuge to process the overflow of the medium-speed centrifuge, remove the ultra-fine particles in the drilling fluid, recover the precious oil-based drilling fluid, and return it to the activated drilling fluid system for recycling.
(4) The combination used in the fourth well section is similar to that in the third well section. The drilling cuttings in the fourth well section are mostly clay particles and sand, which have a great impact on the viscosity of the drilling fluid. Medium and high-speed centrifuges need to be matched in rotation speed, and according to the characteristics of the drilling fluid returned from the bottom of the hole, the centrifuge combination can be used intermittently or continuously to remove ultra-fine harmful solid phases in the drilling fluid and recover barite and oil-based drilling fluid. Among them, the drilling fluid centrifuge combination should adopt variable frequency control. When the drilling fluid viscosity is high, its inlet flow rate is controlled and the rotation speed is increased accordingly to avoid centrifuge clogging and failure. When controlling the flow rate, adjust the speed of the variable frequency centrifuge according to the requirements to reach the highest efficiency point of separation and recovery, efficiently recover barite, and the water-based and oil-based drilling fluids enter the activated drilling fluid system.
The entire solid control system process is optimized and adjusted based on the vibrating screen-centrifuge two-level solid control system. The integrated sand and mud removal machine combined with the underflow screen can not only participate in the solid control system to cooperate with the operation of solid control systems at all levels, but can also be used as backup equipment when the return volume of drilling fluid at the wellhead is too large or the vibrating screen or centrifuge fails. Use: The water-type bottom hole temperature field and viscosity field are significantly better than the simple steam injection method, and can significantly extend the steam huff and puff production cycle. Article source: Chaozhengnijiang
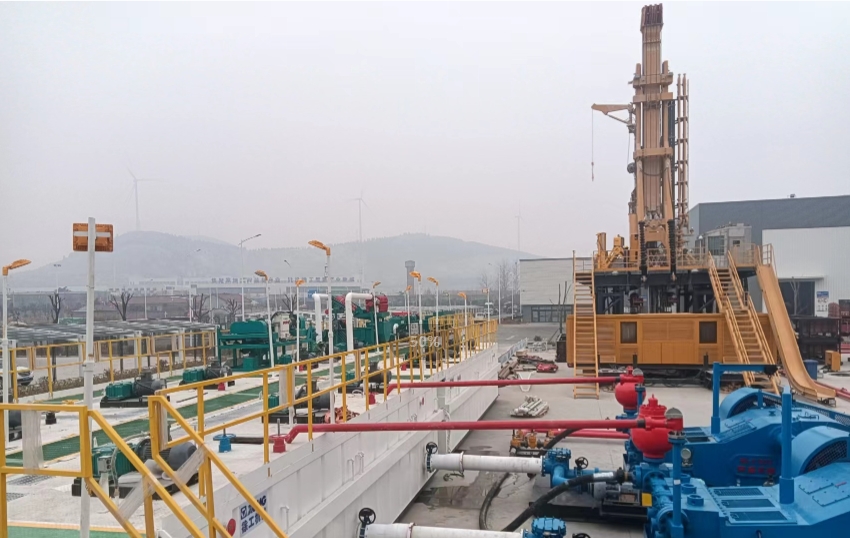
The increase of weighting agent in drilling fluid increases the viscosity and shear force of the drilling fluid, making it more difficult to control the performance of the drilling fluid. Efficient recovery of weighting agents is not only the basic prerequisite to ensure the performance of drilling fluids, but also an effective way to control the cost of drilling fluids.
At present, the effect of using solid control equipment in ultra-deep wells is not ideal. Optimizing the solid control system is an effective measure to improve solid control efficiency and reduce the comprehensive cost of solid control. Based on the research of international scholars, the author has carried out a study on the solid control system of drilling fluid for ultra-deep wells. The rationality of supporting facilities was studied, and the proposed optimized solids control system has significant economic benefits and environmental protection effects.
1. Analysis of solid particles and formation characteristics of drilling fluid system
1.1 Analysis of solid particles in drilling fluid system
Useful solid phases in drilling fluids mainly include bentonite, solid phase weighting agents and additives. To retain useful solid phases and remove harmful solid phases, it is necessary to select appropriate solid control equipment based on the solid phase content and particle size distribution characteristics of the drilling fluid. Therefore, a well-designed solids control process is the basic prerequisite for effective removal of harmful solids and efficient recovery of useful solids.
During the drilling process of deep wells and ultra-deep wells of 4 500 to 9 000 m, barite with a particle size distribution of 10 to 100 μm accounts for more than 80% of the total barite in the drilling fluid; barite with a particle size distribution of 10 to 100 μm Iron ore accounts for about 85% of the total hematite; the bentonite particle size is mainly distributed in the range of 0.01~1 μm. Special attention needs to be paid to recovering weighting agents with a particle size distribution of 10 to 100 μm in solid control systems. Different solid control equipment is selected according to different particle sizes. In the particle size range of 540~800 μm, a 30~50 mesh vibrating screen is used. In the 140~540 μm range, an 80~100 mesh vibrating screen is used. In the 40~140 μm range, a sand remover is selected. , a desilter is used in the 7~40 μm range, and a centrifuge is used in the remaining parts. This kind of matching, whether it is the range of solid phase particle size that various equipment can separate, or the processing capacity of various equipment, is adapted to the solid phase content and particle size distribution of the drilling fluid, and the workload is relatively balanced.
1.2 Analysis of formation characteristics
Taking the 6 000 m and 7 000 m ultra-deep wells in an oil field in China as an example, as the formation depth increases, the drilling fluid density also increases correspondingly, reaching a maximum of about 2.35 g/cm 3 . In ultra-deep wells of 6 000 m and above Weighted oil-based drilling fluid is used to improve the ability to lubricate and carry cuttings to stabilize the well wall and balance the bottom hole formation pressure.
Analyze the particle size and characteristics of drill cuttings in different opening sections. In the upper section of the first and second openings, the formation is shallow, and most solid particles are concentrated in the range of 30 to 300 μm in size, of which more than 80% are particles larger than 200 μm. Large-size solid particles can easily cause drill bit and The wear of the drill string reduces the mechanical penetration rate; in the middle and lower sections of the second opening, the drilling cuttings mostly exist in the drilling fluid in the form of coarse sand grains, fine sand grains, mud grains, etc. Due to the large amount of mud grains, filter cake may be formed. It is easy to cause differential pressure stuck; in the third well section, drilling cuttings particles mainly exist in the drilling fluid in the form of sand grains, mud particles and clay particles, causing reservoir damage and wellbore instability. The barite content in the drilling fluid High, the density is relatively high; in the fourth well section and below, most of the drilling cuttings particles are mud particles and clay particles. The clay particles increase the viscosity of the drilling fluid, resulting in large flow resistance, reduced effective power, reduced drilling speed, and also It is possible for the drill bit to become mud-packed, which increases the range of pressure changes and can easily cause accidents such as spraying, leakage, collapse, and jamming.
Ultra-deep well solids control systems need to efficiently recover high-cost weighting agents, simultaneously process and recover oil-based drilling fluids, and effectively remove harmful solid particles to ensure the safety and smooth progress of the drilling process. This puts relatively high requirements on the performance of ultra-deep well solid control systems.
2. Analysis of oilfield on-site solids control system problems
The four-level solids control system currently used in oil fields (the four-level solids control discussed in this article does not include degasser) has not achieved the expected results. The main problems are as follows:
(1) The Shale Shaker is a full-displacement processing equipment. When the processing capacity of a single unit does not reach the maximum bottom-hole return volume, it is easy to cause slurry running. At the same time, the splashing is serious during the treatment process; the vibrating screen mesh is prone to local damage, resulting in The separation efficiency is poor; after large particles of drill cuttings pass through the vibrating screen, they add extra load to equipment such as desanders, desilters, and centrifuges.
(2) The solid phase removal range of desanders and desilter equipment partially overlaps with that of vibrating screens and centrifuges, resulting in low overall solids control efficiency; the power consumption of the on-site solids control system is approximately 342~370 kW, and the desanders and desilters partially overlap. The power consumption of the mud filter is about 90~150 kW. The power consumption is relatively high, which leads to an increase in drilling costs. The desander and desilter equipment have a high failure rate and are prone to blockage, leakage, drum damage and other failures.
(3) The on-site configuration of the centrifuge is unreasonable, the difference between the combined speeds of the centrifuges is small, and the use effect is not good; the barite content in the removed solid phase is high, resulting in the waste of barite; the ultra-fine harmful solid phase in the drilling fluid Insufficient removal of particles causes the viscosity of the drilling fluid to continuously increase during the circulation process, affecting the normal operation of the entire solid control circulation system and the drilling process; the operation of the centrifuge is not standardized enough and the inlet flow control is not reasonable, resulting in a high failure rate of the centrifuge. .
3. Research and analysis on the reasonable configuration of ultra-deep well solid control system The current solid control process lacks pertinence
As different formations and drilling parameters change, the solids control process should also be adjusted according to the actual situation to achieve the removal and recovery functions of the solids control system in the most reasonable way.
3.1 Optimization design of solid control system
The four-level solids control system is currently the most common solids control system. The system was optimized and designed, and a two-level solid control system based on vibrating screen and centrifuge was proposed. In this system, the sand remover and silt remover are replaced by an integrated sand and mud removal machine, and an underflow screen is added at the bottom. When used, it can not only remove large particles of useless solid phase, but also recover barite particles and drilling fluid. Under normal working conditions, the integrated sand and mud removal machine is used as backup equipment and is not used by the system. When the return volume from the wellhead is large, or the vibrating screen or centrifuge fails, the integrated sand and mud removal machine is used as a backup equipment to process the drilling fluid, so that the entire solid control cycle process is continuous and uninterrupted, reaching the power consumption of the entire solid control system. Low requirements, high modularity and high reliability.
After separation, it enters the parallel multi-layer vibrating screen combination for processing. According to the actual situation, 3 to 5 vibrating screens are connected in parallel. The performance and screen mesh size of a single vibrating screen need to be based on the drilling fluid return volume and drilling fluid particle characteristics of different open section wellheads. If the returning drilling fluid particles have high humidity, a dry vibrating screen can be used if necessary.
3.2 Adaptability analysis of solids control system after optimization
(1) In the first well opening section, most of the drilling cuttings are large particles, and the return drilling fluid has a large displacement. During this period, only the parallel vibrating screen group can be used to remove large particles of cuttings. The mesh number used by the vibrating screen can be selected from 80 to 100 meshes. The separation particle size is greater than 165 μm. The critical separation particle size of the vibrating screen is 180 μm and the minimum separation particle size is 100 μm, which meets the processing capacity of drilling fluid. , and the large particles of drill cuttings were removed, and the discarded drill cuttings particles were directly discharged into the waste solid phase pool.
(2) In the middle and lower section of the second well, a parallel vibrating screen group and a medium-speed centrifuge are used together, and an integrated sand and mud removal machine is used as backup equipment. At this time, the vibrating screen mesh is selected to be 120 mesh or above, and is used with a medium-speed centrifuge or an integrated sand and mud removal machine to remove smaller solid particles in the drilling fluid to prevent them from circulating to the bottom of the well and being repeatedly worn into ultra-fine particles, thus ensuring the normal operation of the equipment. operation, extending the service life of the equipment and improving the safety factor of the entire solid control system.
(3) In the third well section, a parallel vibrating screen group and medium and high-speed centrifuges are used in combination. In this section of the well, the density of the drilling fluid is high and the barite content in the drilling fluid is high. At this time, the requirements for the removal of ultra-fine solid particles in the drilling fluid and the recovery of barite are relatively high, so it is necessary to start a medium-speed centrifuge for recovery drilling. barite in the liquid; start the high-speed centrifuge to process the overflow of the medium-speed centrifuge, remove the ultra-fine particles in the drilling fluid, recover the precious oil-based drilling fluid, and return it to the activated drilling fluid system for recycling.
(4) The combination used in the fourth well section is similar to that in the third well section. The drilling cuttings in the fourth well section are mostly clay particles and sand, which have a great impact on the viscosity of the drilling fluid. Medium and high-speed centrifuges need to be matched in rotation speed, and according to the characteristics of the drilling fluid returned from the bottom of the hole, the centrifuge combination can be used intermittently or continuously to remove ultra-fine harmful solid phases in the drilling fluid and recover barite and oil-based drilling fluid. Among them, the drilling fluid centrifuge combination should adopt variable frequency control. When the drilling fluid viscosity is high, its inlet flow rate is controlled and the rotation speed is increased accordingly to avoid centrifuge clogging and failure. When controlling the flow rate, adjust the speed of the variable frequency centrifuge according to the requirements to reach the highest efficiency point of separation and recovery, efficiently recover barite, and the water-based and oil-based drilling fluids enter the activated drilling fluid system.
The entire solid control system process is optimized and adjusted based on the vibrating screen-centrifuge two-level solid control system. The integrated sand and mud removal machine combined with the underflow screen can not only participate in the solid control system to cooperate with the operation of solid control systems at all levels, but can also be used as backup equipment when the return volume of drilling fluid at the wellhead is too large or the vibrating screen or centrifuge fails. Use: The water-type bottom hole temperature field and viscosity field are significantly better than the simple steam injection method, and can significantly extend the steam huff and puff production cycle. Article source: Chaozhengnijiang