WhatsApp: 86-13735815206 / 86-17392256505
WeChat: 86-13735815206 / 86-17392256505
Phone: 86-29-88680837
Mail: sales@hlsolidscontrol.com
Add: Room 804, Building 1, Western Cloud Valley Phase II, Fengxi New Town, Xixian New District, Shaanxi Province
WeChat: 86-13735815206 / 86-17392256505
Phone: 86-29-88680837
Mail: sales@hlsolidscontrol.com
Add: Room 804, Building 1, Western Cloud Valley Phase II, Fengxi New Town, Xixian New District, Shaanxi Province
HL Petroleum | Automatic Diaphragm Filter Press Product Advantages
Time: 2024-05-06 Source: Author:
Automatic Diaphragm filter press, also known as Automatic Diaphragm Filter Press, is a type of filter press and a common solids control equipment. It presses the material in the filter plate cavity through the bulge and contraction of the diaphragm, so that the liquid phase in the material is squeezed out through the filter cloth, and the solid phase remains on the filter cloth. It is widely used in various industries such as oil drilling, chemical industry, food, pharmaceutical, light industry, mineral processing, coal and so on.
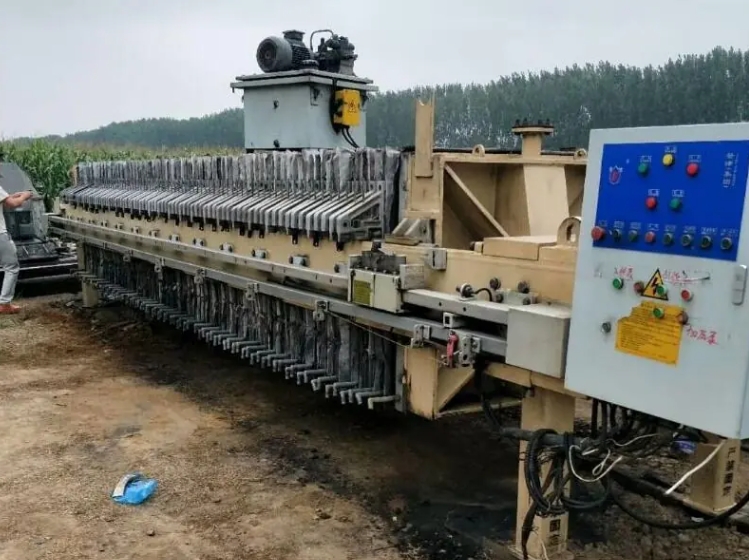
The diaphragm filter press mechanism has a simple structure, high overall sealing performance, good corrosion resistance, small occupied volume, large processing capacity, strong circulation, high filtration accuracy, low leakage probability, easy maintenance, safety and reliability. It can improve efficiency, reduce costs and ensure filtration quality. The Automatic Diaphragm Filter Press is considered to be an alternative and upgraded equipment to the ordinary chamber filter press.
The main difference between the diaphragm filter press and the ordinary chamber filter press is that two elastic membranes are installed on both sides of the filter plate. During operation, when the feeding is completed, high-pressure fluid medium can be injected into the diaphragm plate. At this time, the entire diaphragm will bulge, compressing the filter cake, thereby further dehydrating the filter cake.
The first is positive pressure dehydration, also known as slurry dehydration. That is, a certain number of filter plates are closely arranged in a row under the action of strong mechanical force. A filter chamber is formed between the filter plate surface and the filter plate surface. The filtered material is It is sent into the filter chamber under positive pressure. The solid part of the filter material entering the filter chamber is intercepted by the filter medium (such as filter cloth) to form a filter cake. The liquid part passes through the filter medium and is discharged from the filter chamber, thereby achieving the purpose of solid-liquid separation. As the positive pressure increases, the solid-liquid separation becomes more complete, but in terms of energy and cost, excessive positive pressure is not cost-effective.
After the pulp is dehydrated, a filter press equipped with a rubber extruded membrane will allow the compressed medium (such as air, water) to enter the back of the extruded membrane and push the extruded membrane to further dehydrate the extruded filter cake, which is called extrusion dehydration. After pulp dehydration or squeeze dehydration, compressed air enters one side of the filter cake in the filter chamber to penetrate the filter cake, and carries liquid moisture from the other side of the filter cake through the filter cloth and out of the filter chamber for dehydration, which is called wind-blown dehydration. If there are filter cloths on both sides of the filter chamber, the liquid part can evenly pass through the filter cloths on both sides of the filter chamber and be discharged from the filter chamber, thus dehydrating the filter chamber on both sides.
After the dehydration is completed, the mechanical pressing force of the filter plate is released, the filter plate is gradually pulled apart individually, and the filter chambers are opened respectively to unload the cake. This is a main work cycle to complete. Depending on the properties of the filtered materials, the filter press can be set up for pulp dewatering, squeezing dehydration, wind blowing dehydration or single or double-sided dehydration, with the purpose of minimizing the moisture content of the filter cake.
Classification
According to different diaphragm materials, the new generation of diaphragm filter presses can be divided into rubber diaphragm type and polymer elastomer diaphragm type diaphragm filter presses.
The rubber diaphragm filter press is ideal for filtering materials that are weakly acidic, weakly alkali, and non-organic solvents. The rubber diaphragm filter press changes the shortcomings of the past split fixed type to save energy consumption after feeding. The new design makes the rubber diaphragm more fully used, and the pressure and air volume used are relatively small. Under the same air source and air volume, the rubber diaphragm The eardrum is three times the size of the polymer diaphragm eardrum, which can greatly reduce energy consumption.
Polymer elastomer diaphragm filter press is used for strong acid, strong alkali and organic solvent materials. Its performance is relatively more ideal and its service life is longer. Its pressing forms are divided into gas (air) pressing and liquid (water) pressing, which can meet the needs of different industries. The pressing components can be configured as food grade or ordinary grade according to customer needs, and PLC and human-machine interface can be used for control. For general materials, the squeezing and dehydration function of the diaphragm can be fully exerted after 3-15 minutes. For some special materials, the segmented pressing method of first low-pressure pressing and then high-pressure pressing can also be used.
The Automatic Diaphragm Filter Press realizes a high-efficiency dehydration filtration process and ensures that the filter press can achieve the best filtration effect and significantly reduce the moisture content of the filter cake. After the feeding process is completed, the filter cake is pressed to improve the dehydration efficiency of the entire machine, increase the dryness of the filter cake, reduce pollution and reduce labor. In some processes, the drying process can even be eliminated.
Automatic Diaphragm Filter Presses are more flexible than other filtration forms. Among the four major sludge filter press systems: belt filter press, plate and frame filter press, chamber filter press and Automatic Diaphragm Filter Press, the Automatic Diaphragm Filter Press sludge dewatering is relatively thorough. Automatic Diaphragm Filter Presses are used in sludge and sewage treatment. The minimum moisture content of the filter cake has reached less than 60%. Compared with the traditional chamber filter press, the solid content of the filter cake can be increased by more than 2 times.
HL Petroleum produces various specifications of Automatic Diaphragm Filter Presses. We are a professional solids control equipment manufacturer. HL Solids Control products are professional, reliable, cost-effective and customizable. If necessary, please contact us.
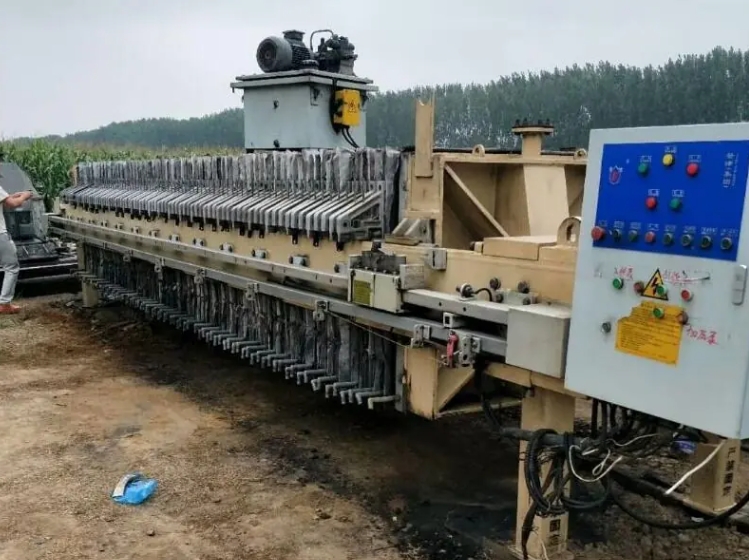
The diaphragm filter press mechanism has a simple structure, high overall sealing performance, good corrosion resistance, small occupied volume, large processing capacity, strong circulation, high filtration accuracy, low leakage probability, easy maintenance, safety and reliability. It can improve efficiency, reduce costs and ensure filtration quality. The Automatic Diaphragm Filter Press is considered to be an alternative and upgraded equipment to the ordinary chamber filter press.
The main difference between the diaphragm filter press and the ordinary chamber filter press is that two elastic membranes are installed on both sides of the filter plate. During operation, when the feeding is completed, high-pressure fluid medium can be injected into the diaphragm plate. At this time, the entire diaphragm will bulge, compressing the filter cake, thereby further dehydrating the filter cake.
The first is positive pressure dehydration, also known as slurry dehydration. That is, a certain number of filter plates are closely arranged in a row under the action of strong mechanical force. A filter chamber is formed between the filter plate surface and the filter plate surface. The filtered material is It is sent into the filter chamber under positive pressure. The solid part of the filter material entering the filter chamber is intercepted by the filter medium (such as filter cloth) to form a filter cake. The liquid part passes through the filter medium and is discharged from the filter chamber, thereby achieving the purpose of solid-liquid separation. As the positive pressure increases, the solid-liquid separation becomes more complete, but in terms of energy and cost, excessive positive pressure is not cost-effective.
After the pulp is dehydrated, a filter press equipped with a rubber extruded membrane will allow the compressed medium (such as air, water) to enter the back of the extruded membrane and push the extruded membrane to further dehydrate the extruded filter cake, which is called extrusion dehydration. After pulp dehydration or squeeze dehydration, compressed air enters one side of the filter cake in the filter chamber to penetrate the filter cake, and carries liquid moisture from the other side of the filter cake through the filter cloth and out of the filter chamber for dehydration, which is called wind-blown dehydration. If there are filter cloths on both sides of the filter chamber, the liquid part can evenly pass through the filter cloths on both sides of the filter chamber and be discharged from the filter chamber, thus dehydrating the filter chamber on both sides.
After the dehydration is completed, the mechanical pressing force of the filter plate is released, the filter plate is gradually pulled apart individually, and the filter chambers are opened respectively to unload the cake. This is a main work cycle to complete. Depending on the properties of the filtered materials, the filter press can be set up for pulp dewatering, squeezing dehydration, wind blowing dehydration or single or double-sided dehydration, with the purpose of minimizing the moisture content of the filter cake.
Classification
According to different diaphragm materials, the new generation of diaphragm filter presses can be divided into rubber diaphragm type and polymer elastomer diaphragm type diaphragm filter presses.
The rubber diaphragm filter press is ideal for filtering materials that are weakly acidic, weakly alkali, and non-organic solvents. The rubber diaphragm filter press changes the shortcomings of the past split fixed type to save energy consumption after feeding. The new design makes the rubber diaphragm more fully used, and the pressure and air volume used are relatively small. Under the same air source and air volume, the rubber diaphragm The eardrum is three times the size of the polymer diaphragm eardrum, which can greatly reduce energy consumption.
Polymer elastomer diaphragm filter press is used for strong acid, strong alkali and organic solvent materials. Its performance is relatively more ideal and its service life is longer. Its pressing forms are divided into gas (air) pressing and liquid (water) pressing, which can meet the needs of different industries. The pressing components can be configured as food grade or ordinary grade according to customer needs, and PLC and human-machine interface can be used for control. For general materials, the squeezing and dehydration function of the diaphragm can be fully exerted after 3-15 minutes. For some special materials, the segmented pressing method of first low-pressure pressing and then high-pressure pressing can also be used.
The Automatic Diaphragm Filter Press realizes a high-efficiency dehydration filtration process and ensures that the filter press can achieve the best filtration effect and significantly reduce the moisture content of the filter cake. After the feeding process is completed, the filter cake is pressed to improve the dehydration efficiency of the entire machine, increase the dryness of the filter cake, reduce pollution and reduce labor. In some processes, the drying process can even be eliminated.
Automatic Diaphragm Filter Presses are more flexible than other filtration forms. Among the four major sludge filter press systems: belt filter press, plate and frame filter press, chamber filter press and Automatic Diaphragm Filter Press, the Automatic Diaphragm Filter Press sludge dewatering is relatively thorough. Automatic Diaphragm Filter Presses are used in sludge and sewage treatment. The minimum moisture content of the filter cake has reached less than 60%. Compared with the traditional chamber filter press, the solid content of the filter cake can be increased by more than 2 times.
HL Petroleum produces various specifications of Automatic Diaphragm Filter Presses. We are a professional solids control equipment manufacturer. HL Solids Control products are professional, reliable, cost-effective and customizable. If necessary, please contact us.